Description
What’s New in FLOW-3D CAST 2023R2
New results file format
Hydrostatic pressure initialization
New Thermal Die Cycling (TDC) model
What’s New in FLOW-3D CAST 2023R1
Advanced features in FLOW-3D CAST 2023R1 allow users to:
- Optimize shot performance, including when making Giga-castings
- Address tooling wear
- Simulate advanced carbon and low alloy steel castings
- Account for the effects of macro-segregation
Plunger motion improvements
We have improved our slow shot calculator to improve accuracy, reduce air entrainment, and expand the range of validity to better handle low fill levels. We also streamlined the user interface, and this combined with the improved slow shot calculator delivers impressive results. You can now easily use data from the slow shot calculator in either plunger position or time-based definitions. The new calculator also provides refined shot profiles that significantly reduce the air entrained at the end of the slow shot.

Expanded PQ2 analysis
Large castings are computationally expensive, and Giga-castings can push a simulation software to its limits. Approximating the shot sleeve and plunger with a velocity boundary condition or metal input is a useful simplification to reduce runtime. However, without PQ2 analysis, it is not possible to know if the HPDC machine is running close to its limits and may not perform as expected, therefore threatening the quality of the part. We have addressed this issue by taking our very capable PQ2 analysis and applying it to metal inputs and velocity boundary conditions. This translates to significant reduction in turnaround times while still maintaining filling accuracy, even in the largest and most complex castings.
Mold erosion prediction
Casting molds and dies wear out for a variety of reasons, including mechanical stressors. Our existing shear load metric is helpful when studying this wear but until now has not accounted for impingement of the metal on the mold and has not been able to predict the final location of sand inclusions in sand casting molds. To address this issue, we added a new output to better understand this wear mechanism. The new output shows the regions where this type of erosion is likely as well as the predicted location of sand inclusions.
Die soldering prediction
Permanent dies used in aluminum castings are subject to chemical wear as the aluminum in the melt bonds to the iron in the die, forming solder that affects the longevity and maintenance needs of the die, as well as part quality. The importance of this wear mechanism led us to build a model that predicts both the location and severity of the soldering.

Chemistry-based carbon and low alloy steel solidification model
The result of one of our longer-term development goals is a powerful, chemistry-based solidification model for carbon and low alloy steels that provide an accurate accounting of the precipitation reactions, solidification and remelting path, and microstructure features and defects. The model also accounts for the important three-phase peritectic reaction and corresponding defects that are associated with the large volume shrinkage due to the delta ferrite to austenite transition.
The model shows excellent agreement with experiments, and provides insights into nonintuitive, time-dependent behaviors, for example, why a hyper-peritectic alloy might develop regions of ferrite at the end of solidification.
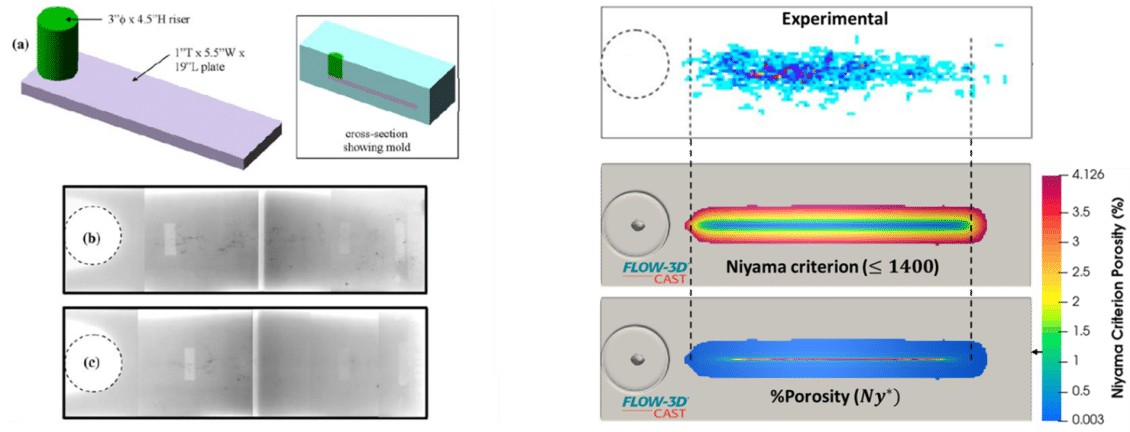
Macro-segregation prediction
Macro-segregation can have an important impact on the quality and downstream processing of castings so we added that to our chemistry-based solidification models. The model predicts where macro-segregation-related defects may occur so you can anticipate and mitigate them before casting.

What’s New in FLOW-3D CAST 2022R2
With the release of the FLOW-3D CAST 2022R2 product family, Flow Science has unified the workstation and HPC versions of FLOW-3D CAST to deliver a single solver engine capable of taking advantage of any type of hardware architecture, from single node CPU configurations to multi-node parallel high performance computing executions. Additional developments include a new log conformation tensor method for visco-elastic flows, continued solver speed performance improvements, advanced cooling channel and phantom component controls, and improved entrained air functionalities.
Unified solver
We migrated our FLOW-3D products to a single, unified solver to run seamlessly on local workstations or on high performance computing hardware environments.
Many users run their models on laptops or local workstations, but in addition run larger models on high performance computing clusters. With the 2022R2 release, the unified solver allows users to exploit the same benefits of OpenMP/MPI hybrid parallelization from HPC solutions to run on workstations and laptops.
Solver performance improvements
Multi socket workstations
Multi socket workstations are now very common and capable of running large simulations. With the new unified solver, users using this type of hardware will generally see performance gains from being able to run models taking advantage of OpenMP/MPI hybrid parallelization that used to be only available on HPC cluster configurations.
Low level routines improved vectorization and memory access
Performance gains on the order of 10% to 20% have been observed for most test cases, with some cases yielding run-time benefits in excess of 20%.
Refined volumetric convective stability limit
Time step stability limit is a major driver in model runtime, with 2022R2, a new time step stability limit, 3D convective stability limit, is available in the numerics widget. For models that are running and convection limited (cx, cy, or cz limits) the new option has shown typical speed-ups on the order of 30%.
Pressure solver pre-conditioner
In some cases, for challenging flow configurations, run times can be drawn out due to excessive pressure solver iterations. For those difficult cases, with 2022R2, when a model iterates too heavily, FLOW-3D automatically activates a new pre-conditioner to help with pressure convergence. Tests have improvements in runtime anywhere from 1.9 to 335 faster!
Log conformation tensor method for visco-elastic fluids
A new solver option for visco-elastic fluids is available to our users, and is particularly effective for high Weissemberg numbers
Active simulation control extensions
Active simulation control functionalities have been extended to include phantom objects, commonly used for continuous casting and additive manufacturing applications, as well as for cooling channels, used in casting and in many other thermal management applications.
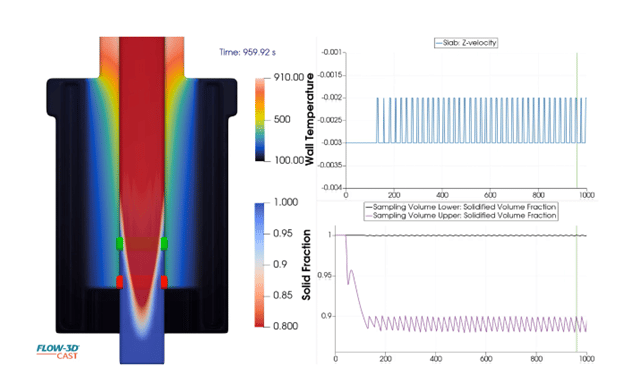