Description
Your CNC Machine digital twin
The MachineMaker app allows you to generate a digital replica of your CNC machine in a matter of minutes. This digital twin is intended for use in programming the CNC machine within the CAD/CAM software SprutCAM X.
Furthermore, MachineMaker features an extensive library of readily available individual components, as well as complete pre-designed digital twins of CNC machines and postprocessors.
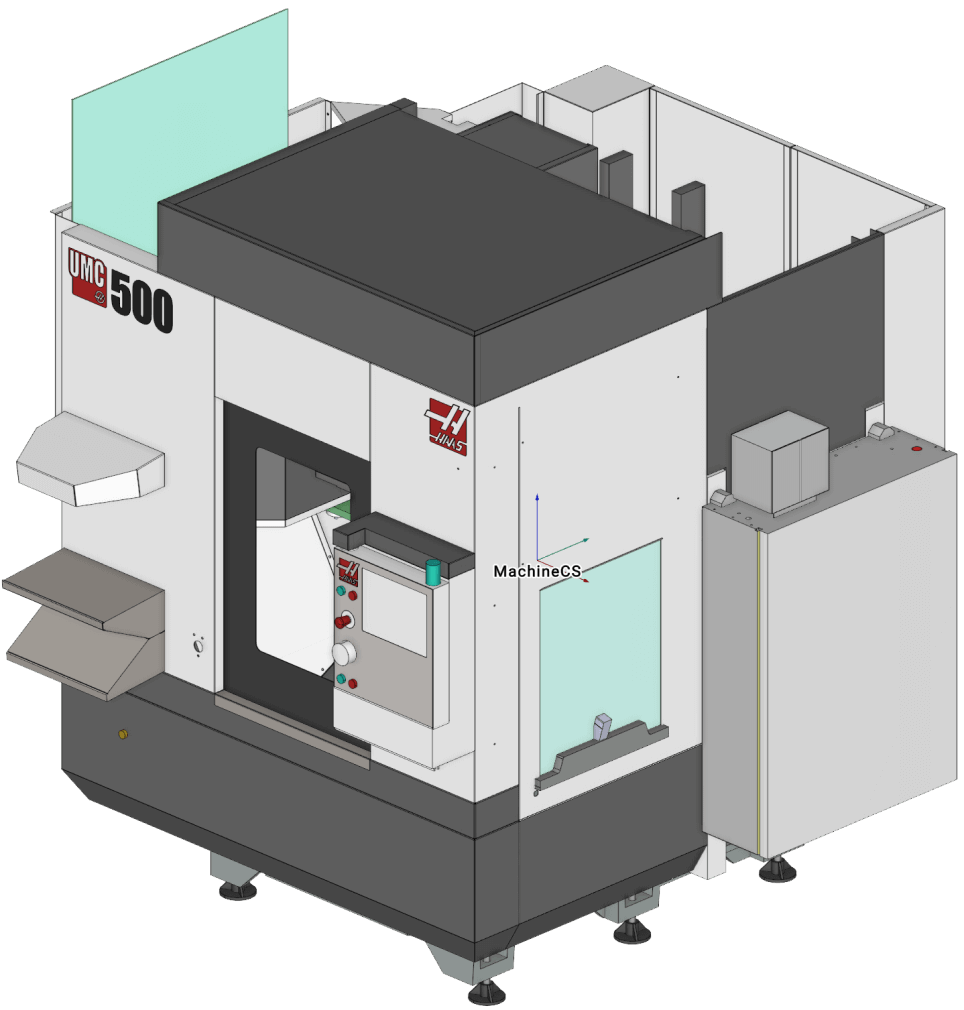
Product Highlights
A wide range of machining strategies from 2D to 5D
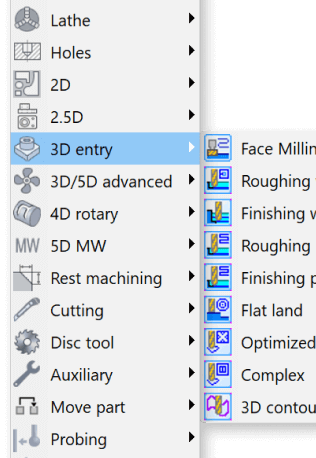
G-code simulation and transformation to other CNC formats
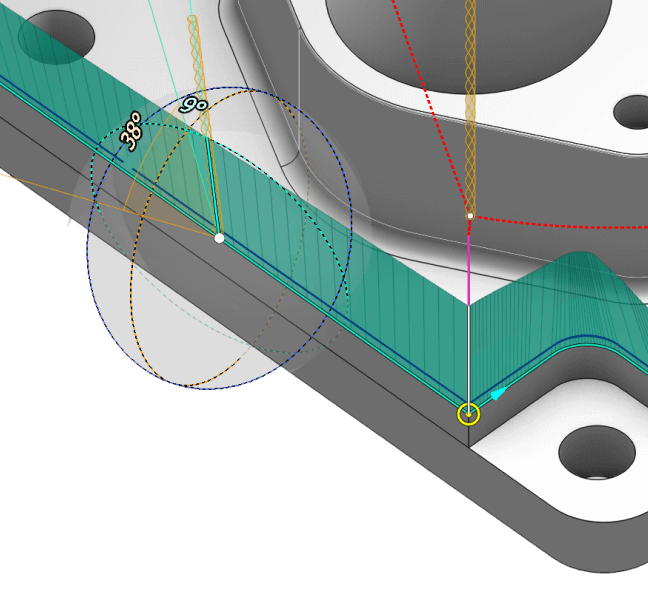
Interactivity
Machining result verification
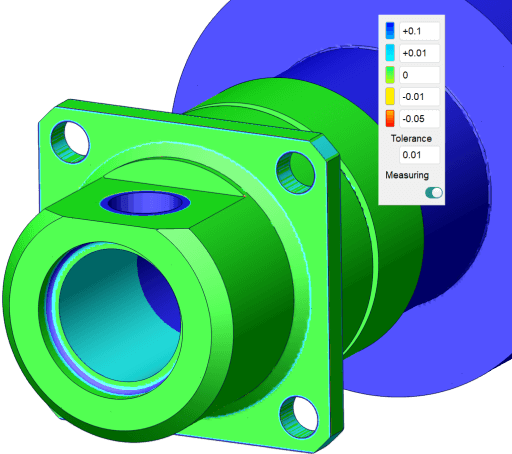
Parametric CAD
Stock-Aware Toolpath
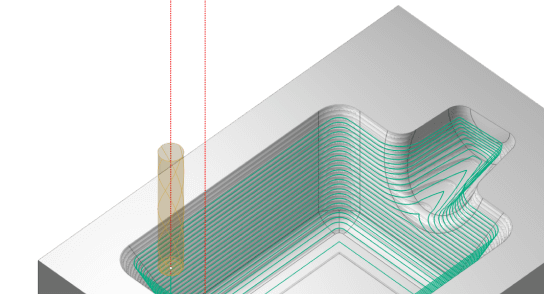
Collision-free rapid positioning between toolpath cutting cycles
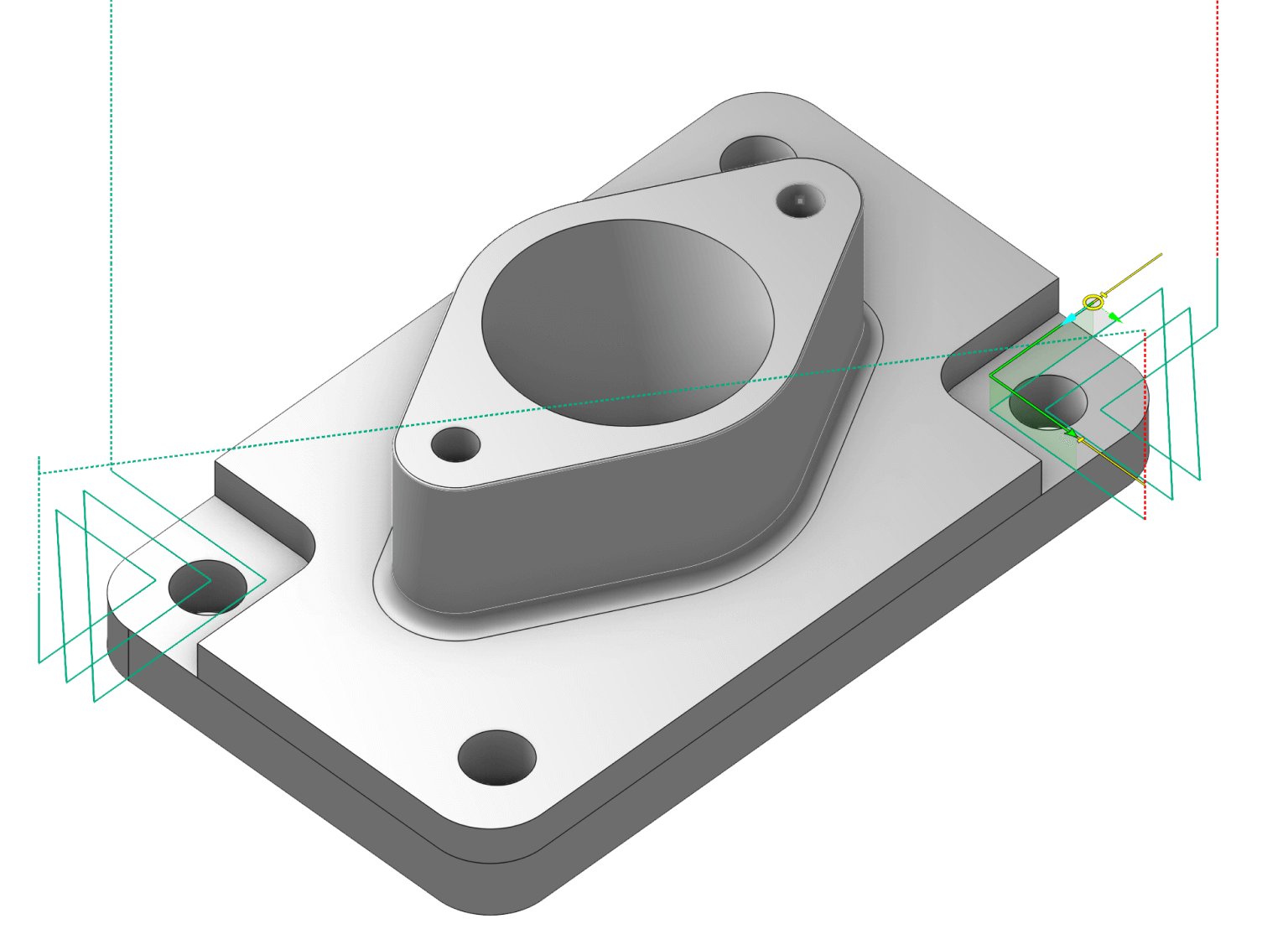
Crisp and clear interface with support of 4K display
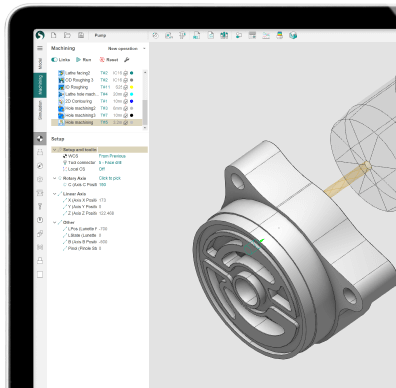
Multi-part projects supported
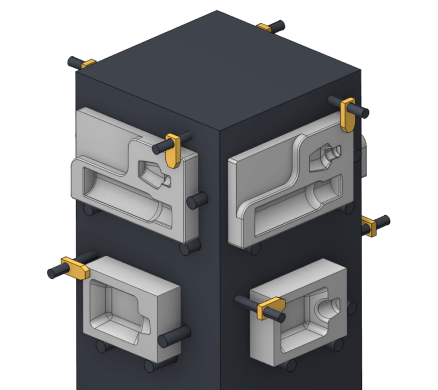
Snapshots
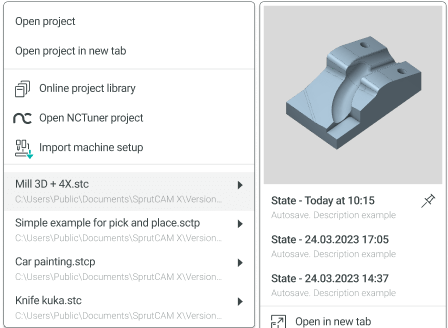
AI Assistant
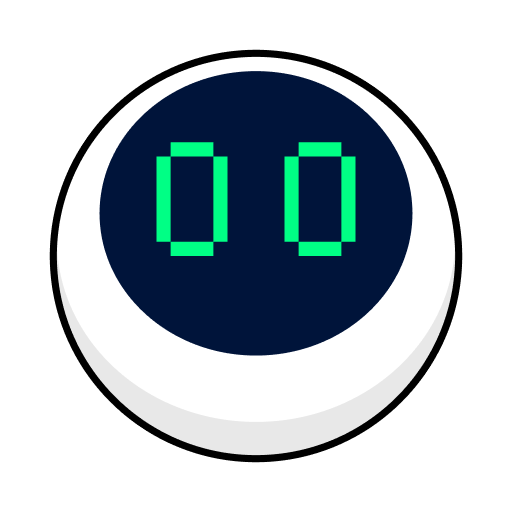
Applications
2.5x and 3x mill
Production of molds & dies and other parts on a 3-axis milling machine
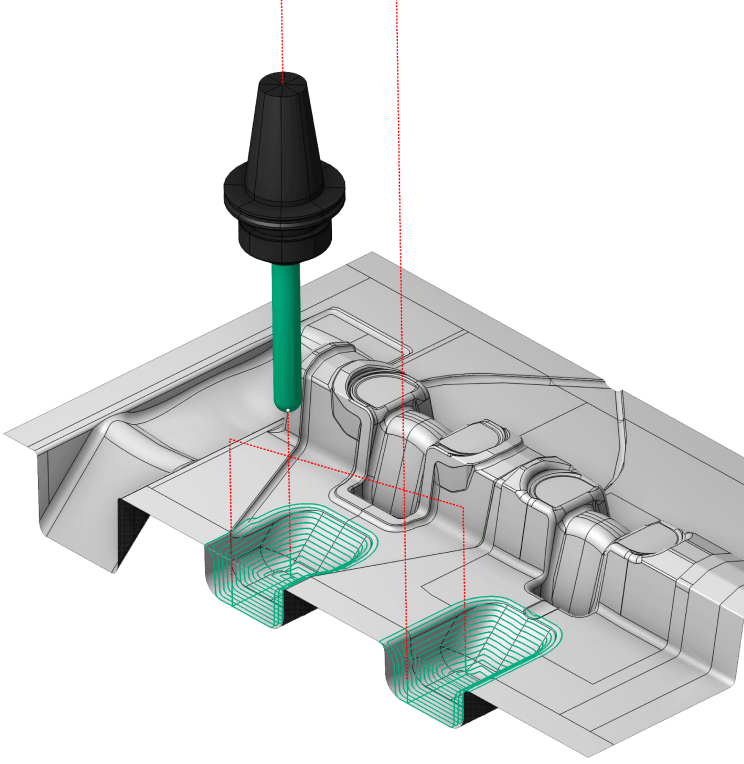
Rotary
Production of screws, blades, gear wheels, balusters
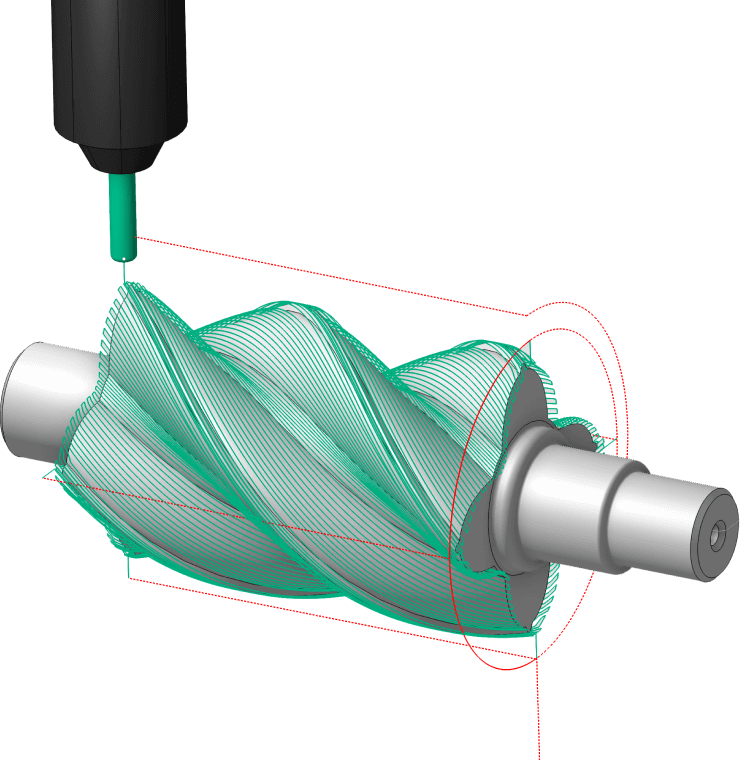
Lathe
Turning and boring, threading, trimming, drilling, reaming
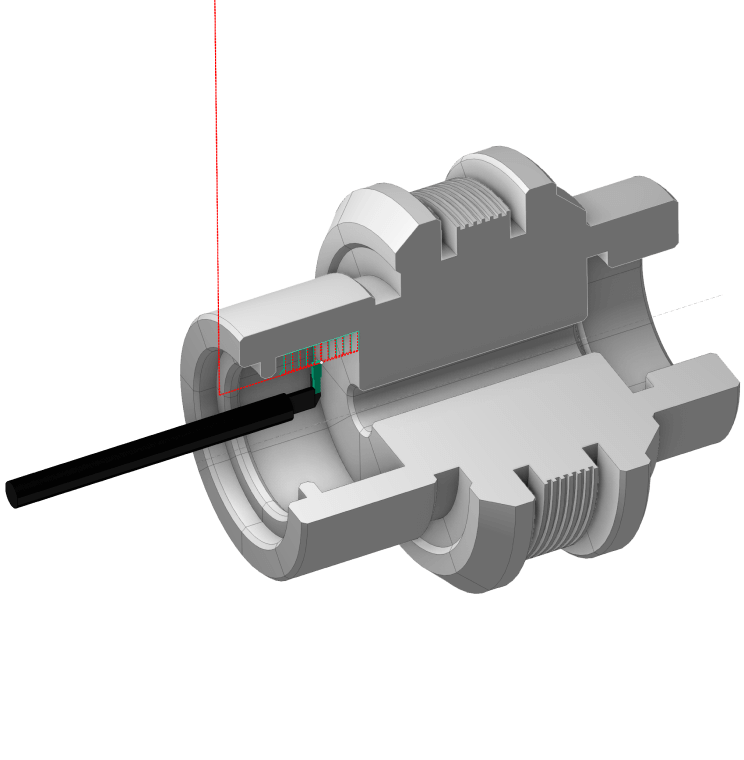
Mill-turn
Turning and milling in one setup
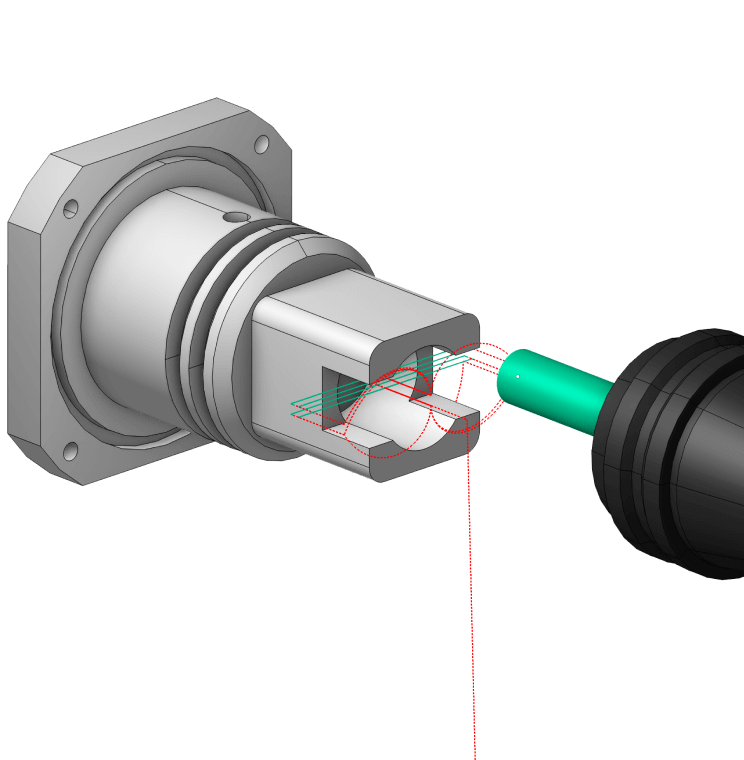
Multiaxis
Index (3+2) and simultaneous 5 axis milling. For turbine wheels, blades, ports
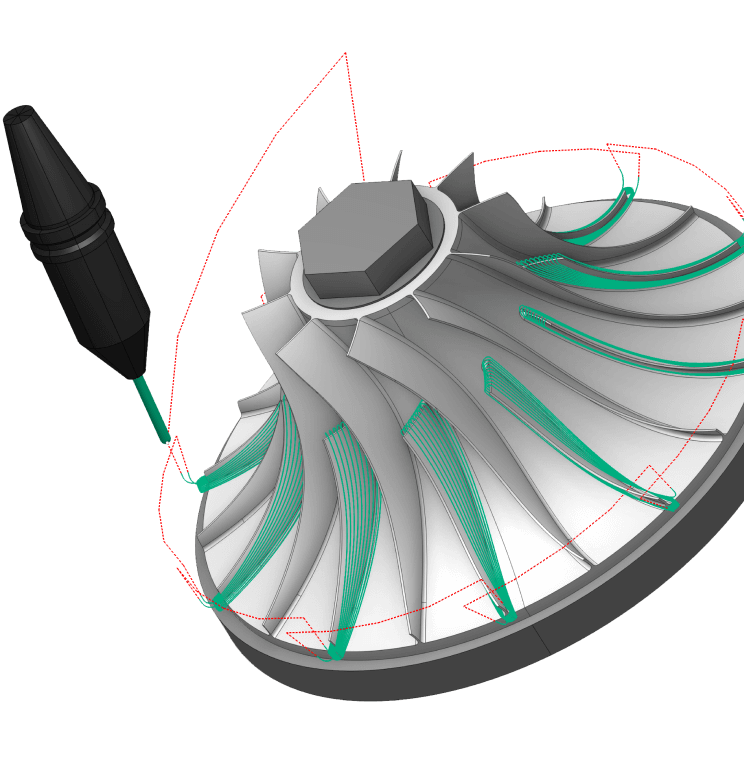
HSM and adaptive
High speed and adaptive toolpaths for quick material removal with extended tool life
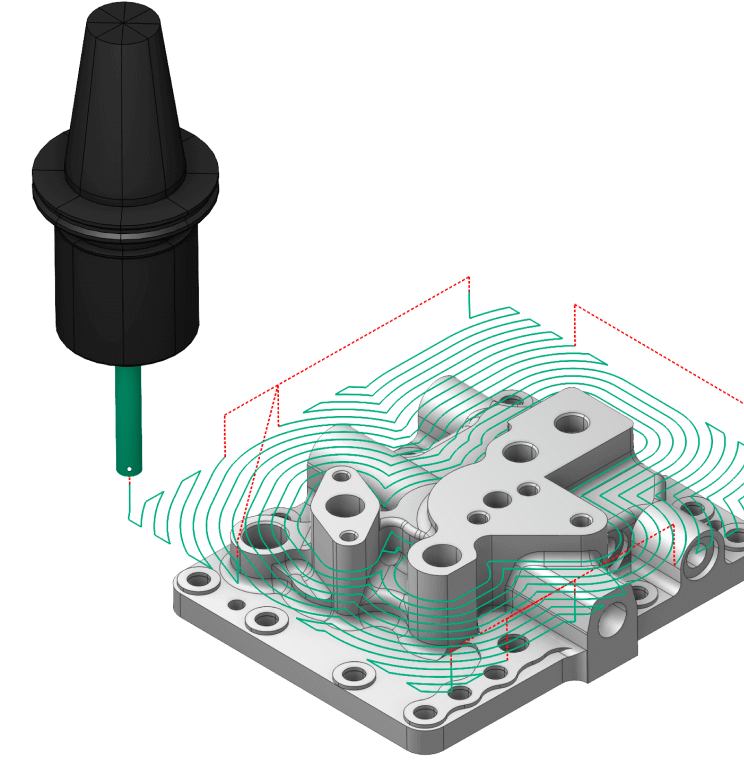
Swiss and MTM
Swiss-type machines and MTM (multitasking machining) with synchronization
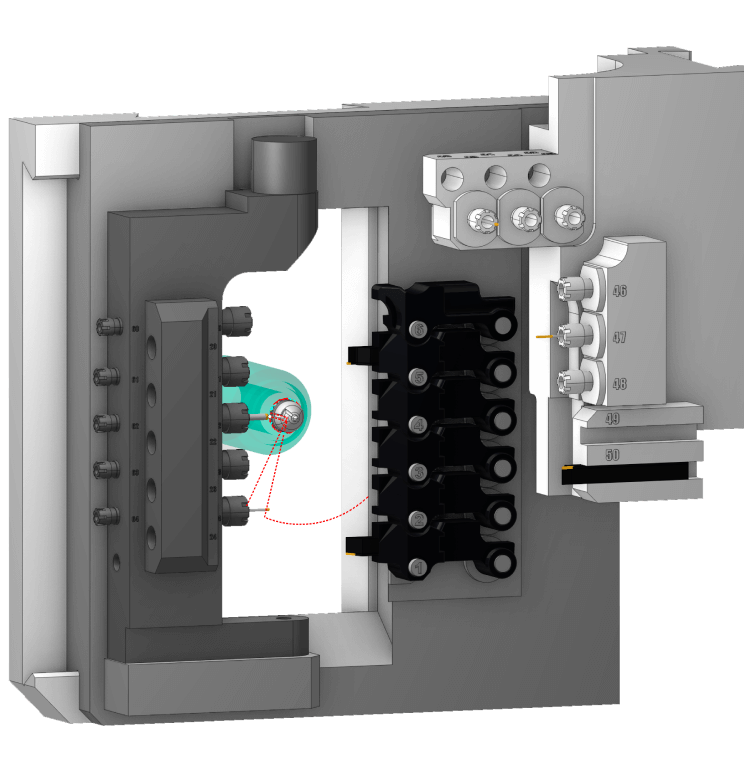
5-6D cutting
CNC programming of cutting, trimming, 6D knife cutting. Mill, laser, water, plasma, knife
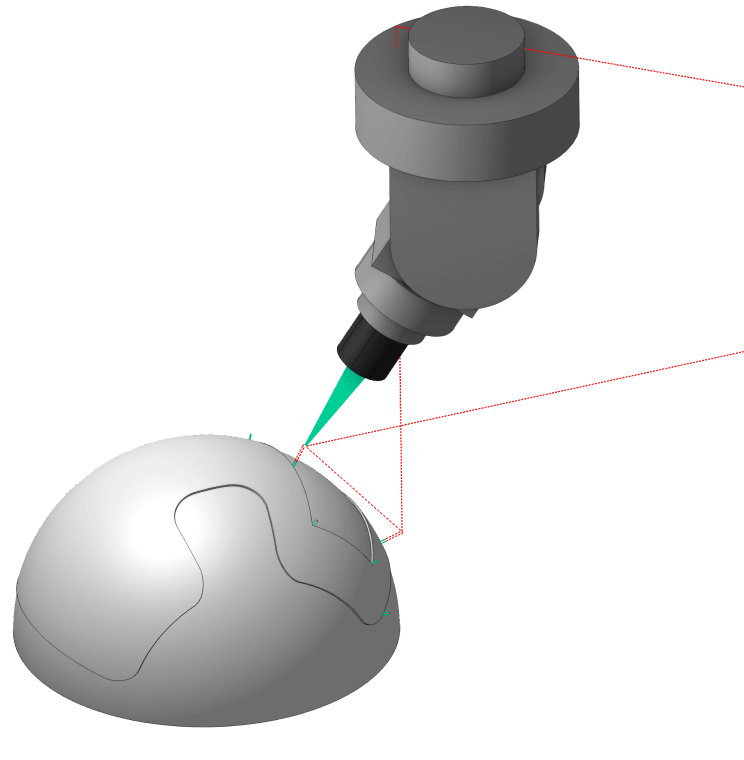
Additive and hybrid
Cladding, hybrid technology on 5-axis, mill-turn machines and robots
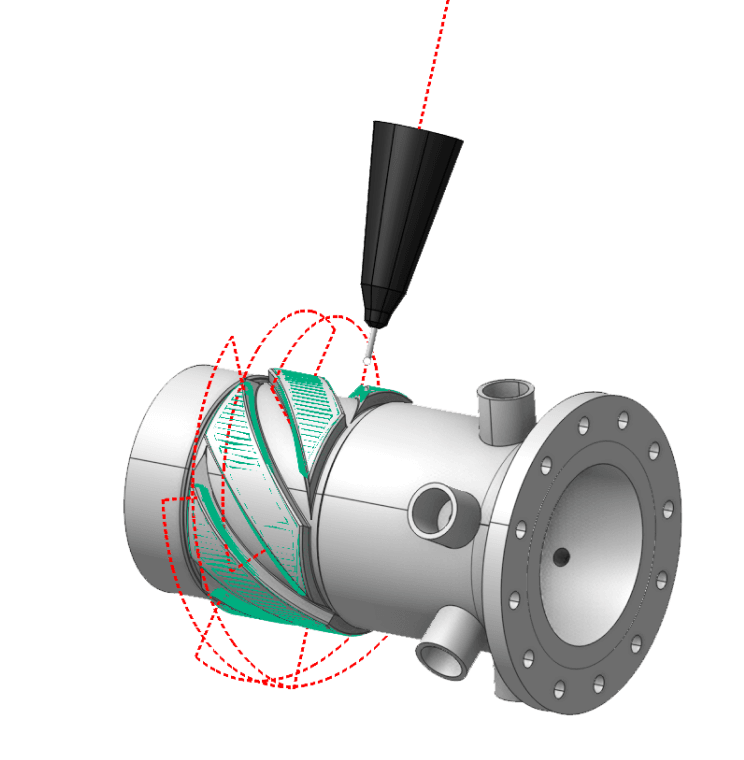
EDM
2 – 4 axis strategies for Wire EDM machining
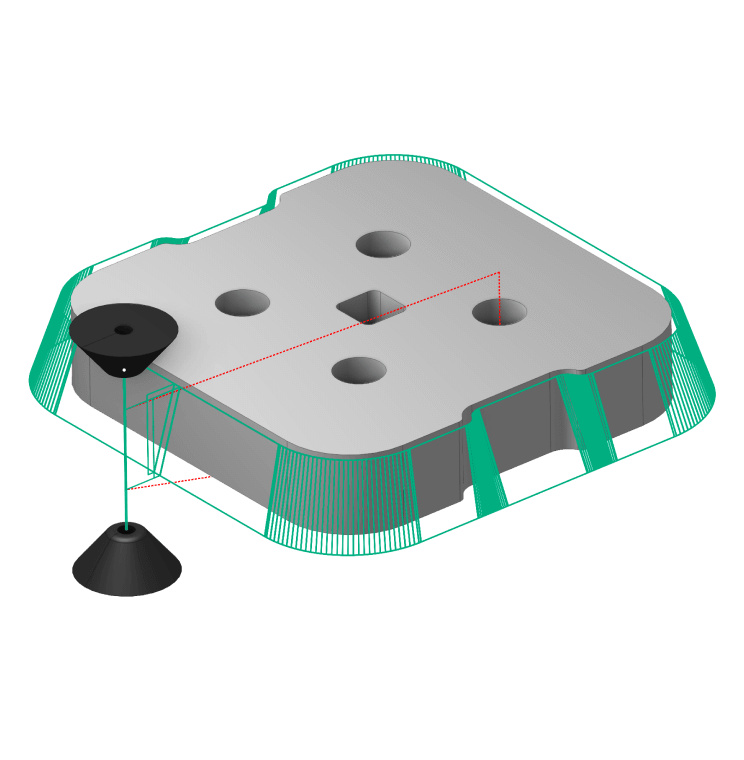
2D cutting
Programming of laser, waterjet, plasma, oxy-fuel cutting and knife cutting
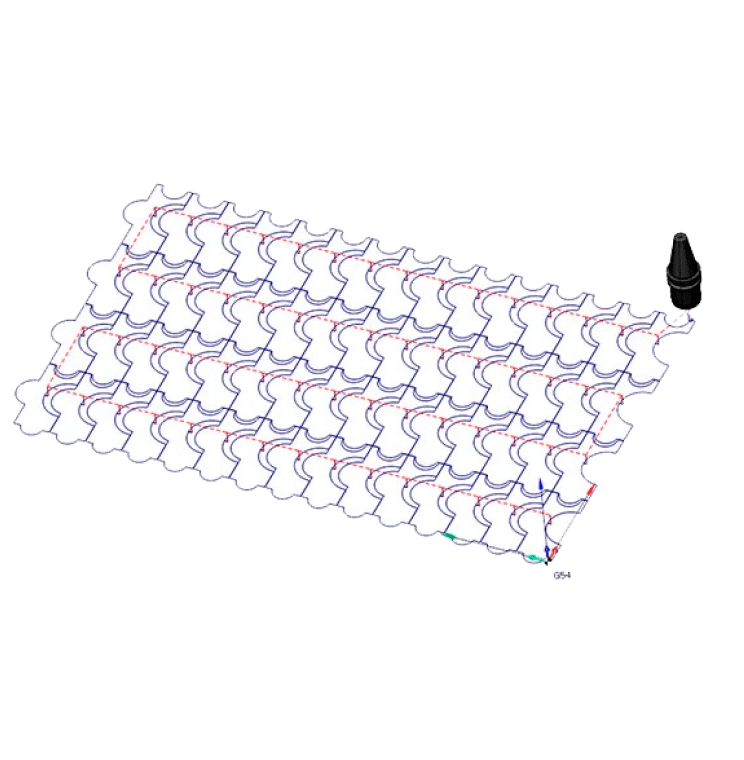
G-code based simulation
G-code verification in SprutCAM
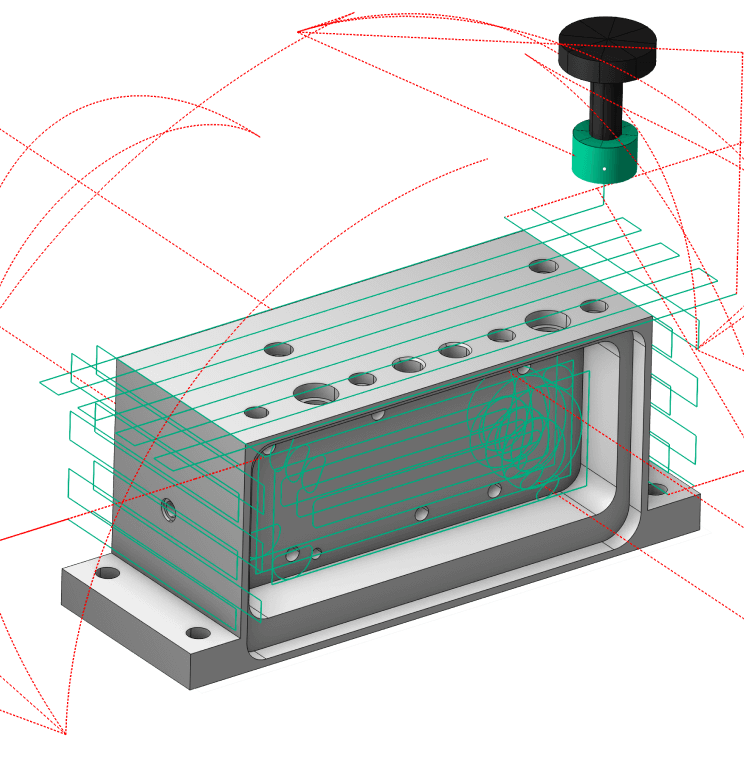
Probing cycles
Probing cycles for Milling and Lathe Machines
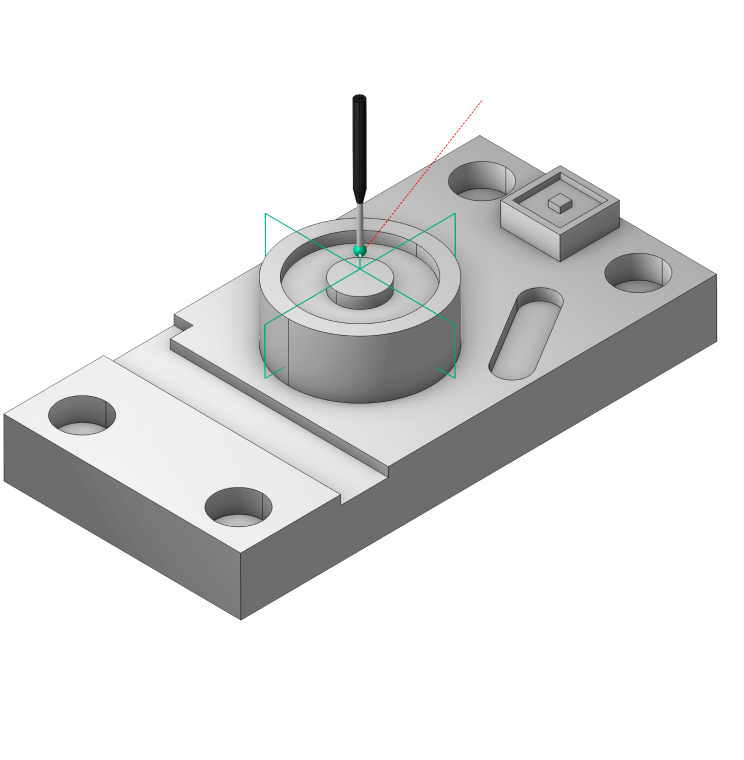
Technology highlight:
Adaptive SC
This high-speed machining cycle is specifically designed for roughing to substantially decrease cycle times and extend tool life. Its technology automatically regulates chip loads and lateral cutting forces while maintaining the cutter engagement angle and machine axes acceleration within optimal ranges.
With Adaptive SC, the machine can make deeper cuts at higher feedrates, which are also automatically optimized throughout the toolpath for maximum efficiency. In comparison to traditional machining methods, Adaptive SC provides the following benefits:
70%
reduction in cycle time
500%
increase in tool life
SprutCAM X is a widely used CAD/CAM/OLP system for CNC machines and industrial robots. We are pioneers in the field of Machine-Aware programming. This technology considers the movement capabilities and limitations of machines and robots at the initial programming stage, unlike most other systems which integrate these considerations during the machining simulation process. This eliminates the need for reprogramming and re-verification, ultimately reducing the time from project initiation to code completion. SprutCAM X is compatible with any CNC machine: 3/4 and 5-axis Mill, Lathe, Mill-turn, Swiss, MTM, EDM. Toolpath calculation considers full machine kinematics and limitations, including collision avoidance and axis limits control. Enjoy the power, speed, and safety of a natural easy to learn, and use CNC programming workflow. SprutCAM X Robot is an innovative all-in-one CAD/CAM/OLP software that allows you to program complex robot applications without disrupting the manufacturing process and the need for an on-site robot programming expert without purchasing a separate CAM system. SprutCAM X Robot supports various brands and configurations of industrial robots, allowing the user to work in a single interface for programming and simulation and output code for use in actual robotic cell applications. Experience the powerful all-in-one software suite for complex and creative robotics tasks.
What’s new in SprutCAM X 17
General improvements
Interface – new popup dialogs design.
Project Snapshots
Snapshots by events
New project extension – “.stcp”
Machine setup file to create new projects quicker
Project library
Multiproject workflow
Technology updates
Improvements in roughing waterline
Redundant axes optimizer improvements
Added display of periodic rotary axes overturns
Arbitrary machine parameter control using map (optimizer)
Singularity avoidance for the 2-axis rotary table of the robot
Point Pick and Place operation added
Links in basic milling operations improved
Scallop operation toolpath enhanced
New undercut waterline operation added
Undercut tools support in 5D Surfacing operation.
Added slope zone in 5D Surfacing operation
New group of operations added – Spray
Approach/return for the TCPM enabled operations using Local CS
Added new parameter for chip breaking in Roughing lathe cycle
Postprocessing and G-code simulation
.NET postprocessors for G-code simulation
Upgrade to .NET 6.0 version
Tool for creating new interpreters
MachineMaker improvements
CAD enhancements
Design module enhancements
Visual overhaul and better user experience
Full-fledged work with the model history
New 3d modeling operations
New sketching tools
Better stability and performance
New CAD import capabilities
Minor changes
Main application executable file changed
New item ‘Duplicate’ in the context menu of the list of technological operations
Post Processor generator
New Trailing zeros output option in Registers
Search in all commands and subprograms
2D arrays and records
Report generation
New features
Selection items for output in the report
Adding customer parameters for each project tree node
Tuning images for the each project tree node
Helper for pattern creation commands
Output operations by setups