Description
Collaborative simulation provides engineers with unique, more complete, and comprehensive performance insights by coupling multiple simulation disciplines together. With the help of MSC CoSim, multibody dynamics (MBD), computational fluid dynamics (CFD), and structural analysis (FEA) can be interconnected. Depending on the type of analysis, engineers can use Hexagon’s solution in two ways – collaborative simulation (applying multiple physical simulations to the model simultaneously) or chain simulation (transferring load situation results from one analysis to the next).
Depending on the type of analysis, engineers can use MSC solutions in two ways – collaborative simulation (applying multiple physical simulations to the model simultaneously) or chain simulation (transferring load situation results from one analysis to the next).
1. MSC Collaborative Simulation Engine
The development purpose of the MSC CoSim engine is to provide a collaborative simulation interface for direct coupling between different solvers/disciplines and multi physics frameworks. MSC CoSim enables engineers to establish collaborative simulation models between Adams, Marc, MSC Nastran, scFLOW, and scTREAM.
2. Other open collaborative simulation solutions
In addition to the CoSim engine, Hexagon also supports a range of other collaborative simulation methods, including Functional Simulation Interface (FMI), Adams Marc Collaborative Simulation Interface (ACSI), and more.
About MSC CoSim 2023.2 :
Hexagon is proud to announce the availability of MSC CoSim 2023.2 as an application strongly supporting multiphysics solutions to enhance your productivity and aid smart manufacturing. MSC CoSim enables coupling between two or more Hexagons CAE solutions: Adams-Marc, Adams-scFLOW, Adams-scSTREAM, Marc-scFLOW, MSC Nastran-scFLOW, Adams-Marc-scFLOW and Marc-scSTREAM. Allowing you to simulate complex real phenomena such as flow through a reed valve or the aeroelastic behavior of an aircraft wing.
Release Highlights in MSC CoSim 2023.2 :
Introducing sub-cycling and sub-steps in MSC Nastran to Cradle CFD scFLOW for faster and robust co-simulation.
The sub-cycling capability allows a considerable speed-up in FSI analyses with MSC Nastran and scFLOW, as one no longer needs to perform the lengthy CFD iteration for each FEA iteration, enabling robust coupling between the codes for static cases.
Considering an aerodynamic analysis of an aircraft wing, this new capability enables the user to perform a non-linear static FE analysis coupled with a steady-state CFD analysis and use multiple sub-steps in MSC Nastran to ensure that each simulation code can have optimal time steps.
Small glider aircraft with flexible wings
How the loading between MSC Nastran and scFLOW works using sub-cycling; in this case, MSC Nastran takes simulation cycles for every scFLOW cycle, and the load is passed from CFD from the two last steps in the FEA at the sub-cycles.
Further, using the MSC Nastran sub-step functionality now allows the user to change loading easily and constraints in the FEA simulation during a co-simulation.
Restarts for Adams to Marc for faster co-simulation analyses.
Co-simulation can be a lengthy analysis, and breaking them into sections can dramatically reduce the time it takes to study multiple scenarios with an identical start but a different ending. One can now perform an initial pre-loading simulation in the FEA to MBD co-simulation and subsequently study multiple load cases without running the pre-loading part more than once.
Overview
Co-simulation provides engineers with a unique, more complete & holistic performance insight by coupling together multiple simulation disciplines. Multibody dynamics (MBD), Computational Fluid Dynamics (CFD), and structural analysis (FEA) can be connected thanks to MSC CoSim. Depending on the type of analysis, engineers can use Hexagon’s solutions in two ways – Co-Simulation (applying multiple physics to the model simultaneously) or Chained Simulation (passing load case results from one analysis to the next).
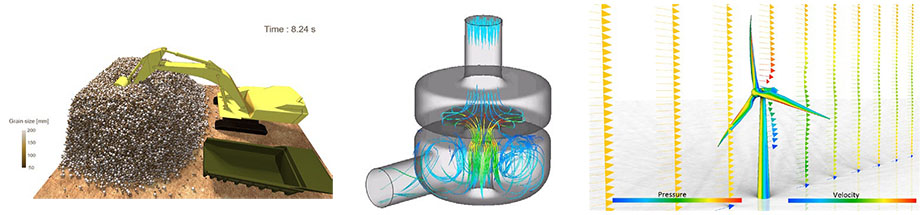
Increased accuracy and precision
“The ability to quickly and easily look at alternatives with co-simulation at a time when we are not locked into any particular approach should make it possible to meet performance requirements with a lighter suspension that can improve the fuel economy of the vehicle.” – Technical Expert at Endurance Attribute and Chassis CAE Department, Volvo
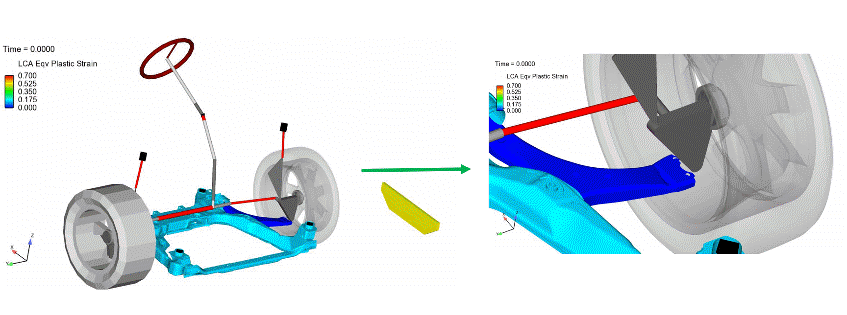
Faster analysis performance
“The Adams-Marc co-simulation capability more than satisfies our guideline of ‘reasonable results in a reasonable time.’ With up to a 90% reduction in computation time, optimization using advanced nonlinear FEA becomes practical. Such development provides a great benefit and is crucial for our product development and we are proud to work together with MSC in advancing the technology.” – Chief Engineer, Litens Automotive Group
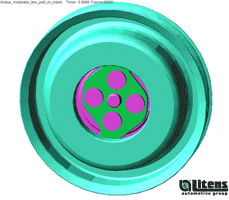
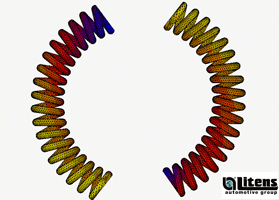
MSC Co-Simulation techniques
Depending on the type of analysis, engineers can use MSC solutions in two ways – Co-Simulation (applying multiple physics to the model simultaneously) or Chained Simulation (passing load case results from one analysis to the next).
1. MSC CoSim engine
The MSC CoSim engine has been developed to provide a co-simulation interface for the direct coupling of different solvers/disciplines with a multiphysics framework. MSC CoSim enables engineers to set up co-simulation models between Adams, Marc, MSC Nastran, scFLOW and scSTREAM.
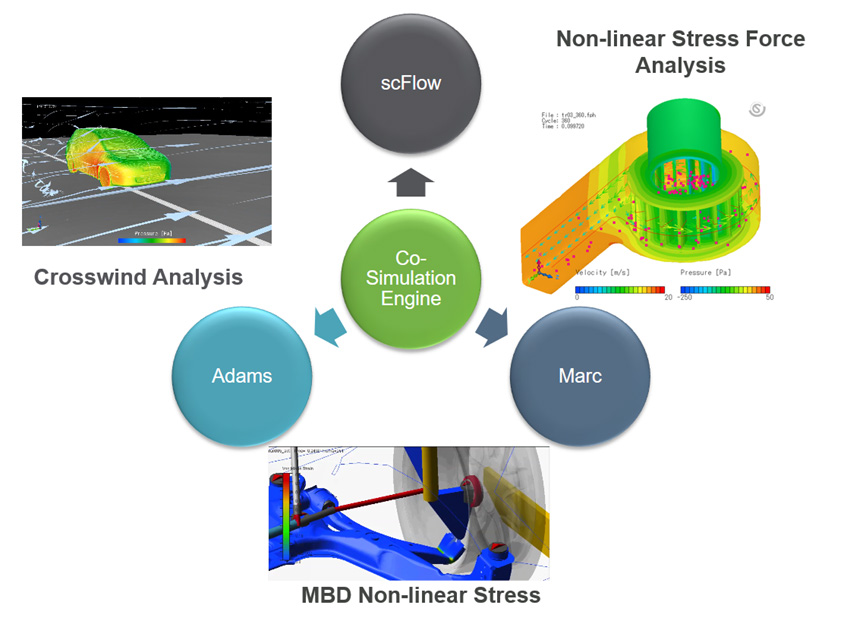
2. Other open co-simulation solutions
Besides the CoSim engine, Hexagon also supports a list of other co-simulation methodologies, including the Functional Mock-up Interface (FMI), Adams Marc Co-Simulation Interface (ACSI) and so on.
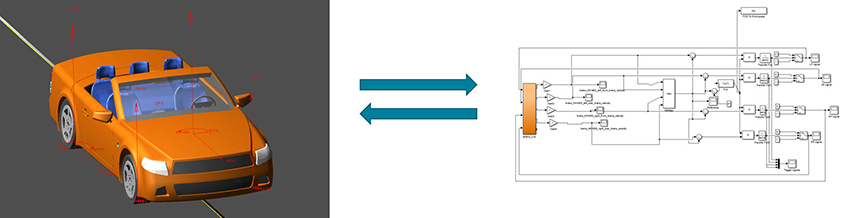
3. Chained simulation
Chained simulation allows CAE engineers from different departments to integrate multiple disciplines sequentially and improve the overall simulation accuracy. For example, passing the road loads data from an Adams Full Vehicle model to the downstream MSC Nastran model for the stress and durability analyses.
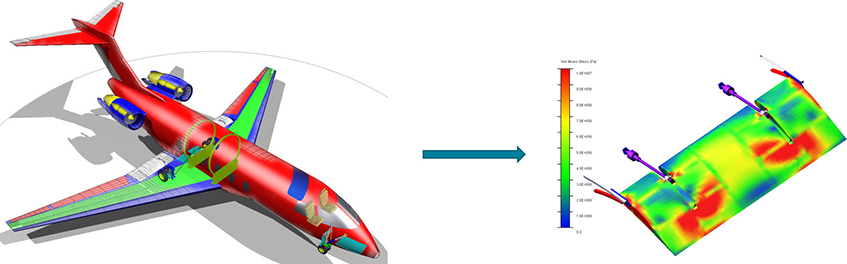